FR4 PCB

What is FR4?
FR4 is a composite material made from woven fiberglass cloth combined with an epoxy resin binder. It is one of the most common base materials used in printed circuit boards (PCBs). The “FR” stands for “flame retardant,” and the “4” refers to its grade for flame resistance.
FR4 is an essential material in nearly every PCB because of its affordability and ease of use. Understanding its properties ensures you choose the best material for your specific PCB manufacturing needs. At Mars PCB, we help you design and manufacture top-quality PCBs tailored to your application.
How is FR4 Used in the PCB Industry?
FR4 serves as the primary insulating substrate in PCBs, providing a strong base to support copper traces that form the circuits. This fiberglass-reinforced material is known for its mechanical strength and excellent electrical insulation, ensuring reliable PCB performance.
FR4 sheets are bonded with copper foil using heat and adhesive, creating a strong and durable connection. The copper layers are etched to create the desired circuit patterns. This process allows for the creation of single-sided, double-sided, or multilayer boards.
Multiple FR4 layers, along with copper, are laminated together with insulating prepreg materials, enabling the creation of intricate and high-density circuits for advanced electronics.
After copper etching, a protective solder mask is applied to prevent oxidation and solder bridges during assembly. Common surface finishes include HASL (Hot Air Solder Leveling), ENIG (Electroless Nickel Immersion Gold), and OSP (Organic Solderability Preservatives).
Halogen-Free PCBs
The most commonly used material, offering a balanced mix of mechanical, electrical, and thermal properties. With a glass transition temperature (Tg) of around 130°C to 140°C, it's suitable for general-purpose applications.
This version is designed for high-temperature environments, with a Tg between 170°C and 180°C. It’s ideal for high-power and high-reliability applications like automotive systems and power electronics.
This material is optimized for RF and microwave use, with a lower dielectric constant and dissipation factor. It minimizes signal attenuation and enhances signal integrity in telecommunications, aerospace, and radar systems.
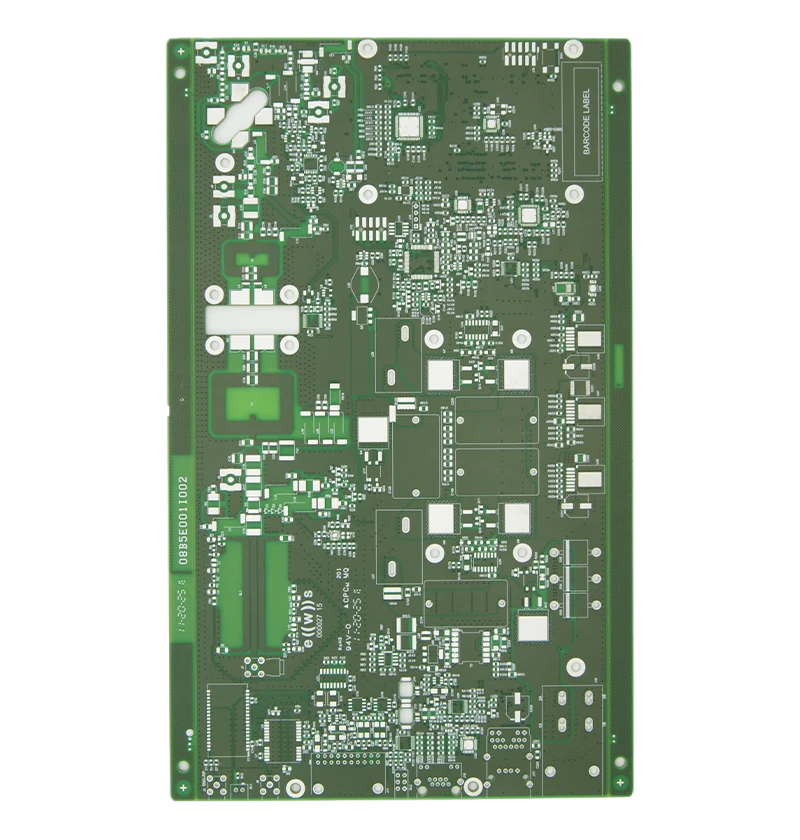
High Comparative Tracking Index (CTI) FR4 offers superior resistance to electrical breakdown and better thermal conductivity. It's perfect for applications requiring quick heat dissipation, such as power supplies and industrial electronics.
Known for its toughness and high resistance to thermal shock, G10 is used where robust mechanical and dielectric properties are needed. While FR4 is flame retardant, G10 is not.
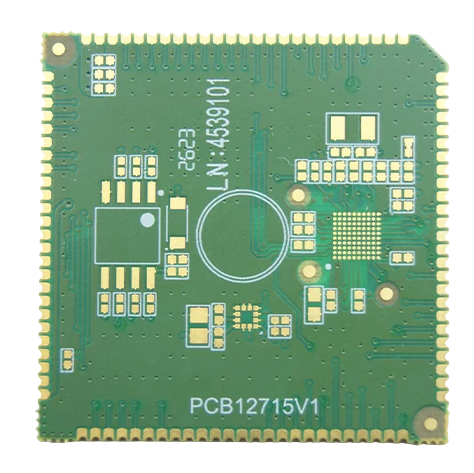
Rogers PCB Applications
FR4 substrates offer important qualities that make them versatile for many electronic applications.
- Mechanical Strength: FR4’s high mechanical strength ensures durability and resistance to physical stresses during manufacturing and use.
- Electrical Insulation: FR4’s excellent electrical insulation prevents electrical shorts, ensuring reliable circuit operation.
- Low Moisture Absorption: Its low moisture absorption helps maintain the material's electrical and mechanical properties even in humid environments.
- Thermal Resistance: FR4 can withstand high temperatures, making it ideal for applications with heat dissipation concerns.
- Flame Retardant: As a flame-retardant material, FR4 reduces the risk of fire, improving the safety of electronic devices.
- Cost-Effectiveness: Compared to other high-performance materials, FR4 offers a cost-effective solution.
Dielectric Properties of FR4
In FR4, the dielectric constant (Dk) measures the material’s ability to store electrical energy in an electric field. The dielectric constant affects how fast electrical signals can travel through the material.
A stable dielectric constant is crucial for maintaining signal integrity, especially in high-frequency applications. This ensures consistent signal propagation and reduces signal loss.

FR4 typically has a dielectric constant (Dk) ranging from 3.9 to 4.8. Depending on the manufacturing process, slight variations may occur. Key impacts of this Dk include:
- Signal Speed: A higher Dk slows down signal propagation. For high-speed circuits, this must be carefully considered.
- Impedance Control: Dk affects the impedance of transmission lines, crucial for maintaining signal integrity in high-frequency applications.
- Loss Tangent: A lower loss tangent (Df) reduces signal attenuation and heat generation, boosting PCB performance.
The dielectric constant can vary based on several factors:
- Resin Composition: Different resin formulations affect Dk values and the electrical performance of FR4.
- Frequency: The dielectric constant typically decreases as the frequency rises, which is important for high-frequency designs.
- Moisture Absorption: Moisture can increase the dielectric constant, affecting PCB performance in humid environments.
- Temperature: As the temperature rises, the dielectric constant decreases, potentially impacting signal integrity in temperature-sensitive applications.
Thermal Properties of FR4
The Tg of FR4 indicates the temperature range where it transitions from a rigid to a more flexible state. Typically, this range is from 130°C to 180°C. Exceeding this temperature can compromise the material’s properties and cause failure.
The CTE measures how much FR4 expands with temperature. FR4’s low CTE ensures stability during temperature fluctuations, but it increases above Tg. This can cause mechanical stress in applications with high thermal demands.
FR4 has relatively low thermal conductivity, typically between 0.25 to 0.4 W/m·K. This means it doesn't dissipate heat as efficiently, so thermal management strategies such as heat sinks and vias are crucial.
After copper etching, a protective solder mask is applied to prevent oxidation and solder bridges during assembly. Common surface finishes include HASL (Hot Air Solder Leveling), ENIG (Electroless Nickel Immersion Gold), and OSP (Organic Solderability Preservatives).
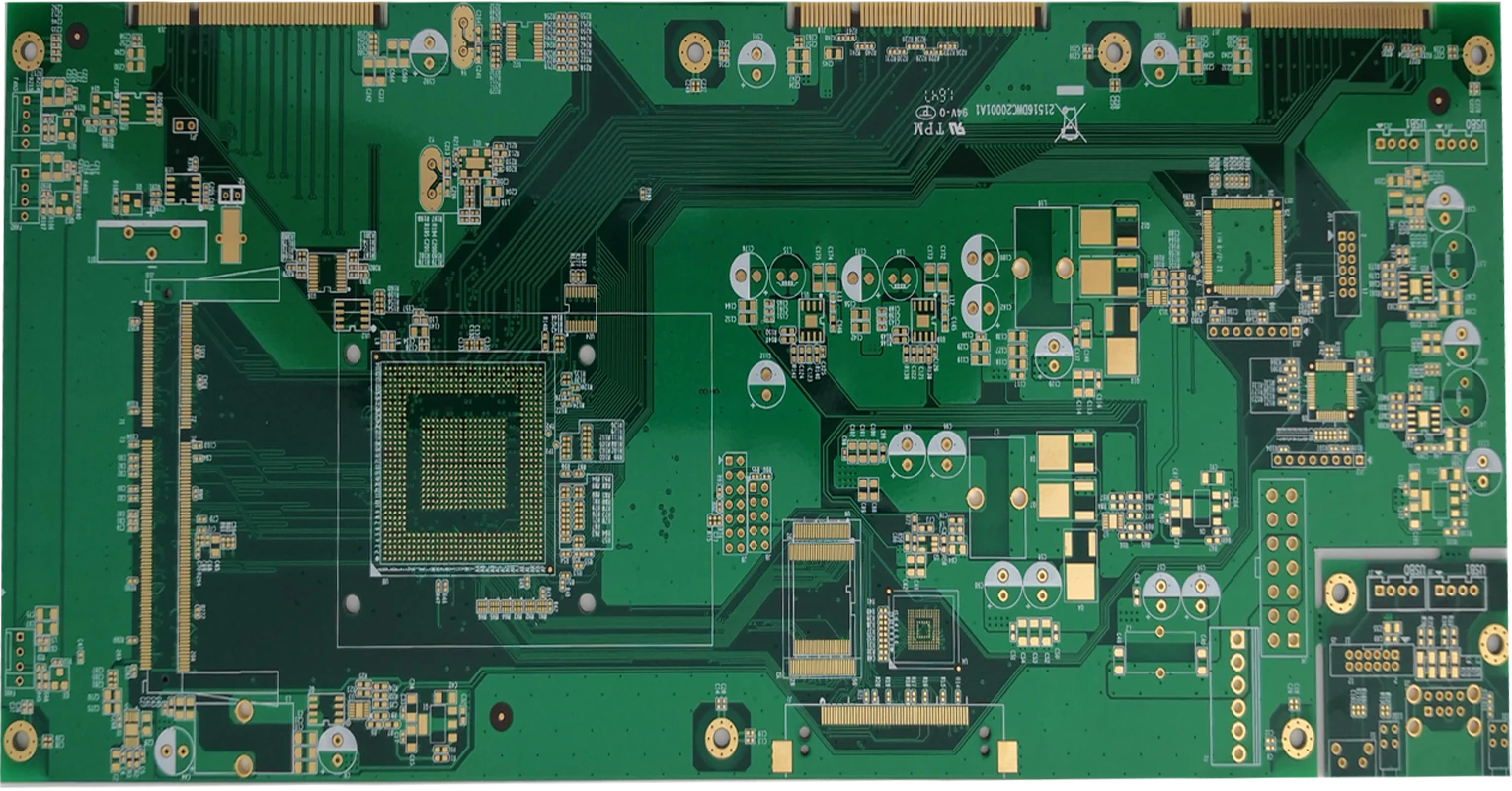
Mechanical Properties of FR4
- Tensile Strength: With a tensile strength of 70,000 psi, FR4 is highly durable and resistant to breakage under tension.
- Flexural Strength: FR4 also boasts a flexural strength of around 70,000 psi, which helps it withstand bending forces without cracking.
- Impact Resistance: FR4 is highly resistant to impact, ensuring durability in harsh environments.
- Dimensional Stability: FR4 maintains its size and shape under various environmental conditions, offering exceptional stability.
FR4 vs. Rogers Material
Feature | FR4 | Rogers Material |
Composition | Woven fiberglass and epoxy resin | Ceramic-filled PTFE composite |
Dielectric Constant (Dk) | 4.2 to 4.6 | 2.2 to 10.2 |
Dissipation Factor (Df) | 0.02 to 0.03 | 0.0009 to 0.002 |
Thermal Conductivity | Handles temperatures up to 130°C | Handles temperatures up to 280°C |
Moisture Absorption | 0.1 to 0.2% | 0.02 to 0.08% |
Advantages | Cost-effective, versatile, flame-resistant | Low signal loss, high-frequency stability |
Disadvantages | Higher signal loss, lower thermal conductivity | Higher cost, complex fabrication |
Applications | Consumer electronics, automotive, industrial | Aerospace, radar, microwave, high-frequency communication |
Cost | Affordable | Higher cost |
Tips to Select the Right FR4 Material
When choosing FR4 material for PCB fabrication, keep these factors in mind:
- Operating Temperature: For high-temperature applications, choose high Tg FR4.
- Thickness Requirements: Select the right thickness for rigidity or flexibility based on your design.
- Electrical Performance: For high-frequency designs, opt for low-loss FR4 with a low dielectric constant.
- Moisture Resistance: For use in humid environments, choose FR4 with good moisture resistance.
- Mechanical Properties: Ensure the selected FR4 can handle mechanical stresses like flexing and expansion.
- Environmental Impact: Ensure the material complies with flame-retardant standards and is durable for long-term use.
- Cost-Performance Balance: Choose the right FR4 based on the balance between cost and performance requirements.
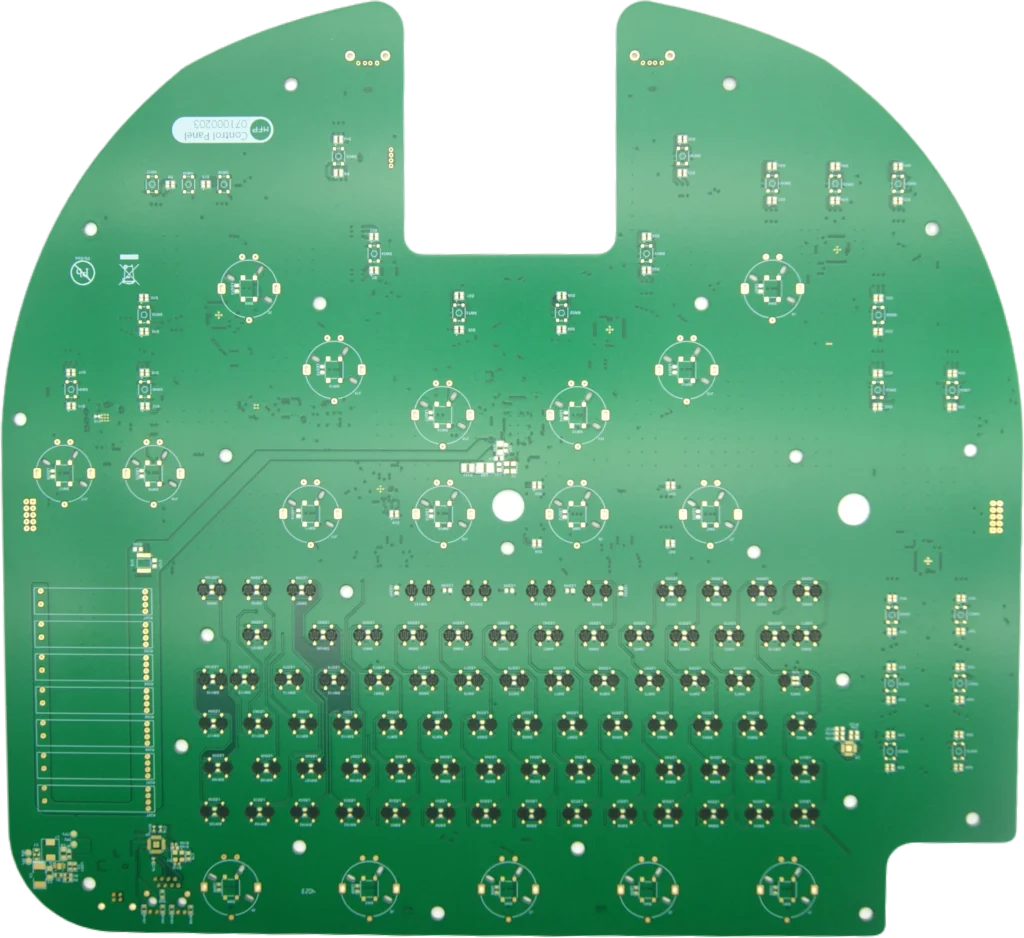
Professional PCB & PCB Assembly Manufacturer & Factory
FR4 is a popular choice for PCB design and assembly due to its versatility and performance. At Mars PCB, we help you select the best FR4 material for your needs, ensuring your circuit boards perform optimally for years.