Teflon PCB: The Comprehensive Guide
Understanding the unique properties of Teflon in PCB manufacturing is essential for creating high-performance, high-frequency circuit boards. At Mars PCB, we specialize in producing a variety of PCBs using advanced materials, including Teflon, ensuring that your products perform reliably in demanding applications. This guide explores why Teflon is a popular choice for PCBs and outlines its key properties and benefits.
What is Teflon PCB?
Teflon PCBs use Polytetrafluoroethylene (PTFE) as the primary material. Sometimes, other PCB materials may be coated with PTFE to enhance their properties. Teflon is known for its low-friction, non-stick surface and chemical inertness, making it highly suitable for high-frequency applications. Its high glass transition temperature (Tg) of up to 280°C is one of the main reasons it is used in the construction of advanced printed circuit boards.
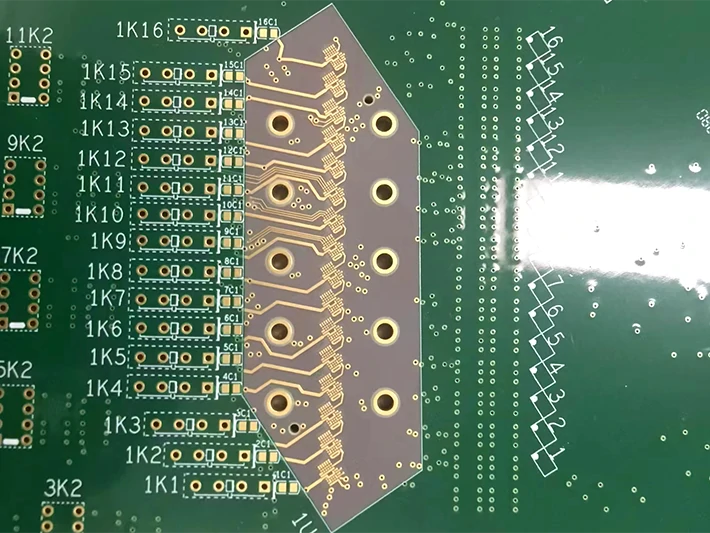
PCB Materials
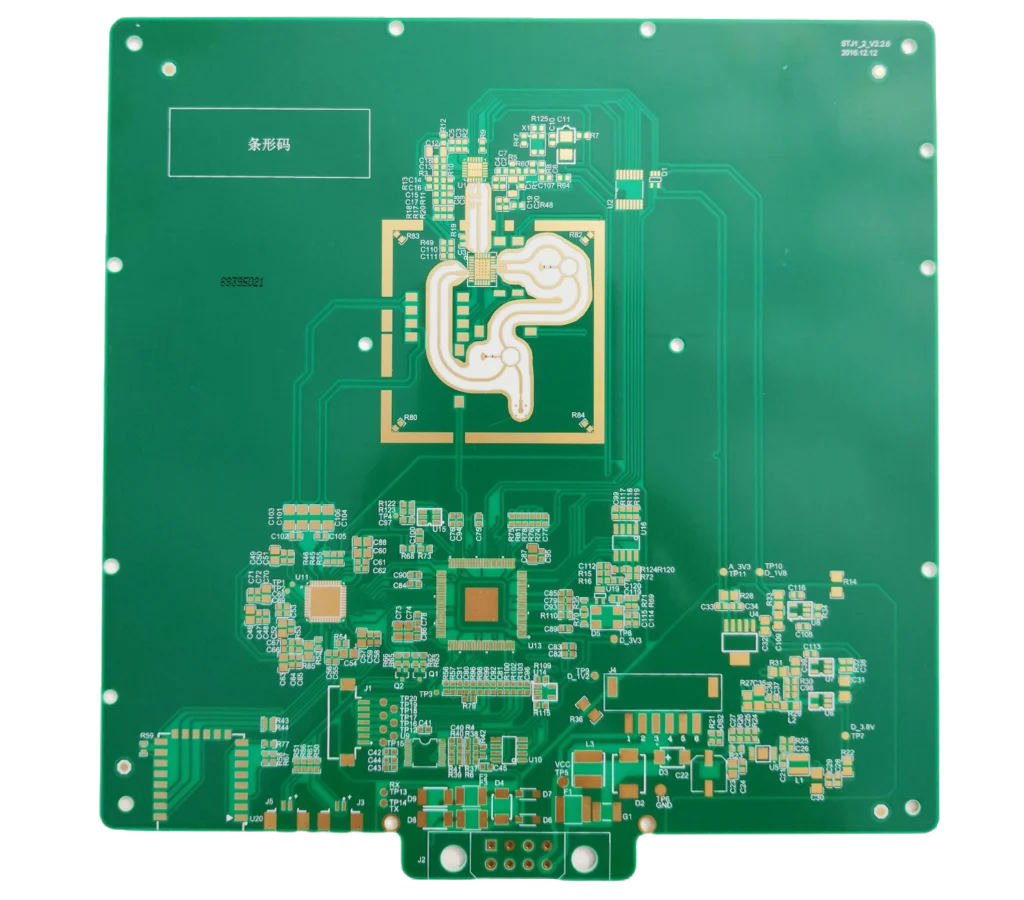
PCB with various components
While Teflon is an excellent material for certain applications, other popular PCB substrates and laminate materials include:
Widely used with a Tg around 135°C. High-temperature versions are available, making them suitable for demanding environments.
These materials are popular for use in high-temperature conditions, with varying Tg points.
Offers low loss and minimal moisture absorption, perfect for high-frequency applications. The Tg is around 315°C.
Other materials like G-10 (fiberglass) and metals such as alumina are also used, but Teflon and FR-4 remain the most common choices for rigid and rigid-flex boards.
Properties and Benefits of Teflon PCBs
The man standing behind an idealized version of AI in the form of a digital PCB
Teflon offers several key advantages that make it a preferred choice for high-frequency PCBs:
- Low Friction: Teflon’s smooth surface results in a low coefficient of friction, reducing wear and tear in applications with moving parts.
- Thermal Stability: With a Tg between 160°C and 280°C, Teflon can withstand high temperatures, making it ideal for electronics that generate significant heat.
- Chemical Resistance: Teflon PCBs resist corrosion from moisture, grease, and chemicals, ensuring longevity and durability.
- Low Dissipation Factor: Teflon’s low dissipation factor ensures minimal signal loss, making it perfect for high-frequency and microwave applications.
- Exceptional Dielectric Properties: The material maintains stable electrical properties even under extreme conditions, ensuring consistent performance.
- High Flame Resistance: Teflon’s resistance to high temperatures and flames makes it suitable for safety-critical applications.
Additionally, Teflon PCBs are mechanically rigid and durable, providing excellent resistance to oxidation and environmental wear.
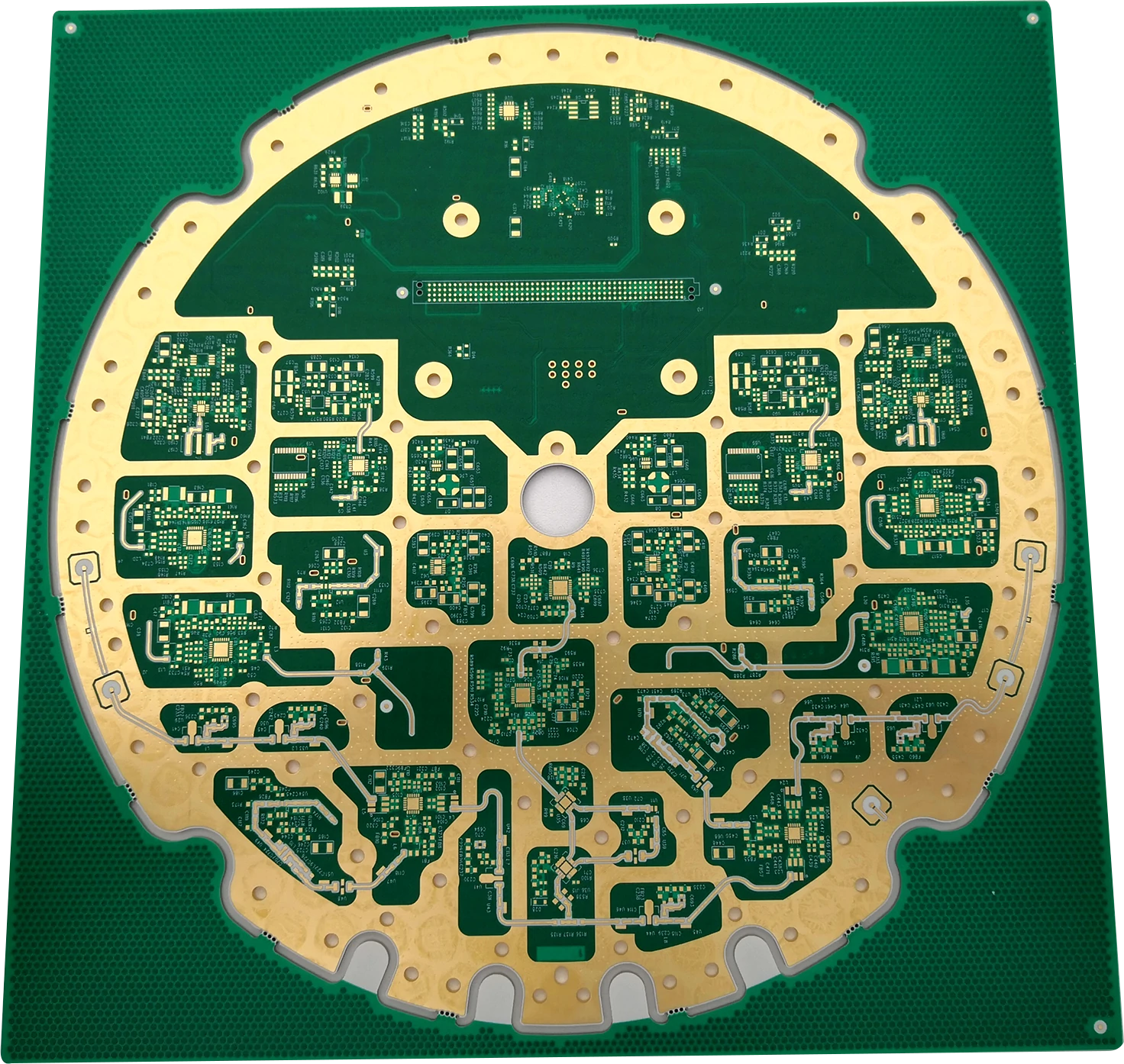
Manufacturing Teflon PCBs: Key Considerations
Manufacturing Teflon PCBs requires specialized techniques to ensure quality and precision.
Teflon requires surface treatment to improve bonding. A sodium etching process is typically used to make Teflon more receptive to bonding, followed by rinsing with alcohol and water.
Teflon laminates are laminated under high temperatures (up to 370°C) and pressures (450-500 PSI). This ensures a solid bond without the need for prepregs or bonding films.
The solder mask should be applied within 12 hours after the etching process to prevent residual moisture from affecting the board.
Special drills with high chip load are used to ensure precise holes and clean cuts, preventing Teflon tailing during the drilling process.
Copper plating is a crucial step in PCB production. High-tensile copper is used to prevent issues like barrel cracks and pad lifting.
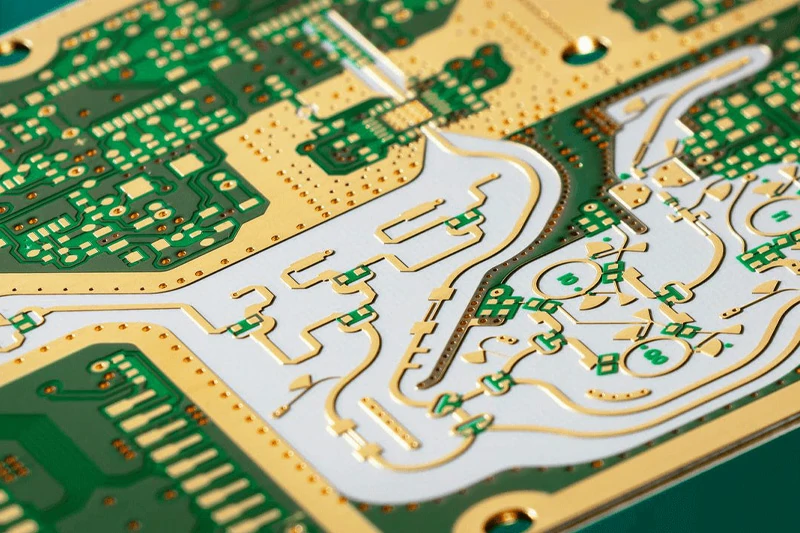
Steps in Producing a Teflon PCB Prototype
The production of a Teflon PCB prototype involves several key stages:
- Design: Create the layout of the PCB using PCB design software.
- Material Selection: Choose the appropriate base material for the prototype. Teflon is often chosen for its specific high-frequency properties.
- Design Testing: Test the design using simulations or an initial prototype board to verify correct connections.
- Troubleshooting: Identify and correct any errors or design flaws in the prototype.
- Prototyping: Build the prototype and conduct thorough testing to ensure it meets specifications.
Applications of Teflon PCBs
Teflon PCBs are used in various high-performance applications due to their durability and ability to handle high frequencies:
- Medical Devices
- Industrial Applications
- Power Amplifiers
- Wi-Fi Routers & Antennas
- Mobile Devices
- Printers
- Radar Systems
- Wireless Base Station
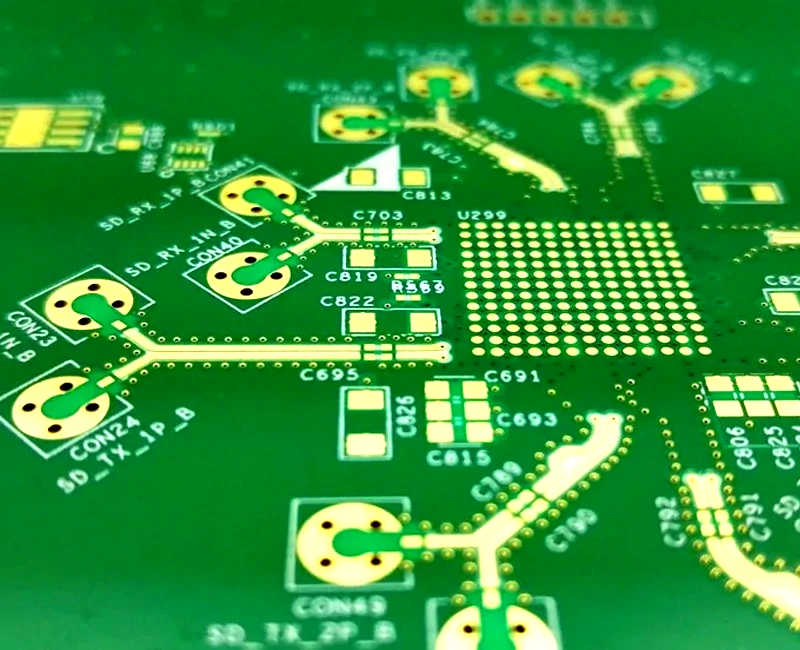
Professional PCB & PCB Assembly Manufacturer & Factory
From concept to completion, your project will be under experienced project management, sparing you the hassle of untimely conference calls, communication gaps, language barriers and “real time” information gathering.