I. Introduction: The Foundation of Multilayer PCBs
In today’s compact and powerful electronic devices, the multilayer PCB stands as a cornerstone of modern design. Unlike simpler single or double-sided boards, multilayer PCBs are composed of multiple layers of conductive traces, precisely separated by insulating dielectric materials and bonded together. This ingenious construction offers significant advantages: it dramatically increases component density, reduces overall product size, and greatly improves electrical performance through enhanced signal integrity and controlled impedance. For any device requiring high functionality in a small footprint, a multilayer PCB is often the only viable solution.
However, the very complexity that gives multilayer PCBs their power also introduces potential vulnerabilities. Among these, delamination stands out as a critical failure mode. This undesirable separation of layers can silently compromise the board’s integrity, leading to a cascade of electrical and mechanical failures that undermine product reliability and shorten device lifespan. For users of multilayer PCBs, understanding both the meticulous art of “stacking” and the insidious threat of “delamination” is absolutely crucial for ensuring product quality and longevity. It empowers you to work more effectively with your multilayer PCB manufacturer and make informed decisions throughout the design and production process.
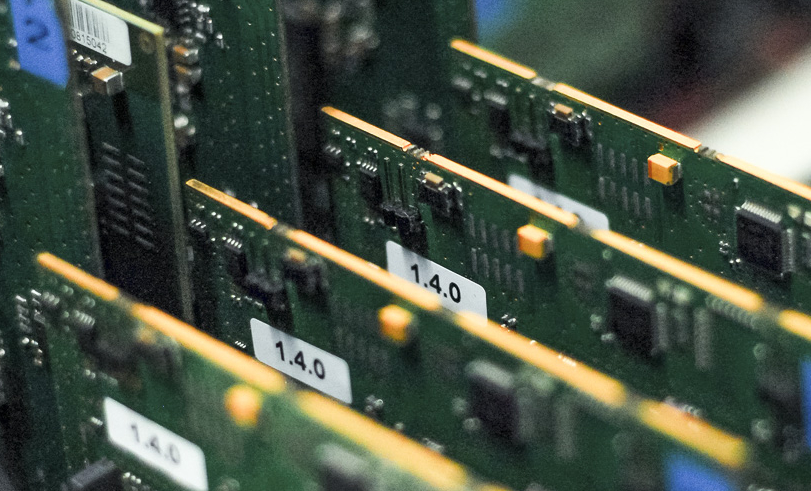
II. Understanding PCB Stacking (Layer Stack-up)
At the heart of every high-performance multilayer PCB is its meticulously planned stack-up. This isn’t just about putting layers together; it’s a precise engineering discipline.
A. Definition and Purpose
A PCB stack-up is the specific arrangement of copper layers and insulating dielectric materials (prepreg and core) in a predetermined sequence. It’s like building a high-tech sandwich, where each layer plays a vital role. The primary purpose of this detailed arrangement is twofold: to achieve precise electrical characteristics necessary for high-speed signals and stable power delivery, and to ensure the overall mechanical integrity of the board.
B. Key Components of a Stack-up
The typical components that form a multilayer PCB stack-up include:
- Cores: These are rigid, pre-laminated sheets of fiberglass-epoxy (most commonly FR-4 material) with copper foil bonded to both sides. Cores provide the fundamental structural stability of the PCB and often house internal signal or power planes.
- Prepreg: This is a “B-stage” material, meaning it’s a fiberglass cloth impregnated with partially cured resin. In its pre-laminated state, it’s soft and pliable. During the multilayer PCB manufacturing process, heat and pressure cause the resin in the prepreg to flow, fill spaces, and then fully cure, acting as both the adhesive between core layers and copper foils, and as the dielectric insulator. The type of prepreg (e.g., standard, mid-loss, low-loss) and its properties (resin content, glass style, dielectric constant (Dk), dissipation factor (Df)) are chosen based on the board’s electrical requirements.
- Copper Foils: Pure copper sheets, typically used for the outer layers (top and bottom) of the PCB. These layers provide the conductive pathways for external components and connections. Internal copper foils are often etched from the copper on core layers to form signal and power planes.
- Solder Mask and Silkscreen: While not part of the internal stack-up, these are external finishes. The solder mask is a protective polymer layer that insulates traces and prevents solder bridges, while the silkscreen provides component legends and markings.
C. Principles of Effective Stack-up Design
A well-designed stack-up is fundamental to the performance and reliability of a multilayer PCB. It’s a critical collaboration between the designer and the multilayer PCB manufacturer.
- 1. Signal Integrity: For high-speed signals, controlling impedance is paramount. A good stack-up positions ground and power planes strategically to act as clear reference planes for signal traces, minimizing signal reflection, crosstalk, and electromagnetic interference (EMI).
- 2. Power Integrity: Stable power delivery is achieved by creating dedicated power and ground planes that provide efficient current return paths and reduce noise and ripple in the power supply.
- 3. Thermal Management: Copper layers efficiently conduct heat. By strategically distributing copper throughout the stack-up, designers can improve the board’s ability to dissipate heat from active components.
- 4. Mechanical Stability: To prevent undesirable warpage and twist, especially during thermal cycling, it’s crucial to balance the copper distribution symmetrically around the board’s center. An unbalanced stack-up can lead to internal stresses.
- 5. Cost Considerations: The number of layers, the type of materials used, and the overall complexity of the stack-up directly influence manufacturing costs. A custom multilayer PCB design needs to balance performance with budget.
D. Common Stack-up Configurations (Examples for Multilayer PCB Users)
Understanding basic stack-up patterns can help in discussions with your multilayer PCB supplier:
Layer Count | Example Configuration | Common Use Cases | Key Benefit |
4-Layer | Signal-Ground-Power-Signal | Simple digital circuits, basic RF applications | Good balance of cost and performance |
6-Layer | Signal-Ground-Signal-Signal-Power-Signal | Medium complexity digital, mixed-signal designs | Better signal integrity with internal signal layers |
8-Layer+ | Multiple Signal/Ground/Power plane pairs, often nested | High-speed computing, complex communication systems | Superior signal integrity and noise reduction |
III. Delamination: The Silent Threat
Despite meticulous design and multilayer PCB manufacturing processes, a significant threat lurks beneath the surface: delamination.
A. Definition of Delamination
Delamination is the undesired separation of layers within a multilayer PCB. This separation typically occurs at the interface between copper and dielectric material (e.g., copper trace lifting from prepreg) or within the dielectric layers themselves. It can manifest as visible blisters, bubbles, or localized swelling on the board’s surface, or as internal separations detectable only through specialized inspection.
B. Types of Delamination
Delamination can present in various forms:
- Internal Delamination: Separation between inner layers, often not immediately visible on the surface.
- External Delamination: Visible separation of outer layers, such as solder mask peeling or the lifting of outer copper traces.
- Localized vs. Widespread Delamination: Affecting a small, specific area versus extending across a large portion of the board.
C. Causes of Delamination
Delamination is a complex phenomenon, often stemming from a combination of factors related to manufacturing, materials, and post-assembly stresses.
- Manufacturing-Related Issues:
- Improper Lamination Cycle: The most common culprit. If the temperature, pressure, or curing time during the multilayer PCB manufacturing process are not precisely controlled, the resin in the prepreg may not fully flow or cure, leading to poor adhesion.
- Poor Material Adhesion: Inadequate surface treatment of inner layer copper (e.g., insufficient roughening or oxidation) can prevent the prepreg resin from forming a strong bond. Poor quality or expired prepreg can also contribute.
- Trapped Volatiles: Moisture or solvents that get trapped within the layers during lamination can expand significantly when exposed to high temperatures (e.g., during soldering), creating internal pressure that forces layers apart.
- Voids/Air Traps: Incomplete resin flow during the lamination process can leave small air pockets, which become weak points prone to expansion and delamination.
- Contamination: Any residue or foreign material on the surface of the prepreg or copper layers can act as a release agent, preventing proper bonding.
- Material-Related Issues:
- Moisture Absorption: Many PCB materials are hygroscopic, meaning they readily absorb moisture from the environment. This absorbed moisture turns into steam at high temperatures (like during multilayer PCB assembly soldering processes), creating immense internal pressure that can lead to “popcorning” or delamination.
- Thermal Expansion Mismatch (CTE Mismatch): Different materials within the PCB (copper, various resin systems, glass fabric) have varying Coefficients of Thermal Expansion (CTE). When subjected to temperature changes, they expand and contract at different rates. If these differences are too great, they create shear stress at the interfaces, especially during repeated thermal cycling, eventually leading to delamination.
- Degraded Material Properties: Prepreg that is over-cured or under-cured, or materials that have been stored improperly (e.g., at high humidity), may have compromised adhesive properties.
- Post-Manufacturing (Assembly & Operation) Issues:
- Thermal Shock: Rapid temperature changes, particularly during reflow or wave soldering in multilayer PCB assembly, can induce severe thermal stress, a common trigger for delamination.
- Excessive Heat: Prolonged exposure to temperatures above the material’s Tg (glass transition temperature, where the resin softens) or Td (decomposition temperature, where the material degrades) can weaken adhesion and lead to delamination.
- Mechanical Stress: Excessive bending, twisting, or vibration of the board during handling, assembly, or operation can also cause layers to separate.
- Component Rework: Repeated heating cycles on specific areas during component rework can severely stress the laminate and increase the risk of localized delamination.
IV. Consequences of Delamination
The ramifications of delamination can be severe, leading to immediate failures or gradual degradation of product performance and reliability.
- A. Electrical Failures:
- Open Circuits: As layers separate, conductive traces or vias (the plated holes connecting layers) can break, leading to open circuits and complete loss of electrical connection.
- Short Circuits: In some cases, uneven delamination can cause conductive traces from different layers to come into contact, resulting in unintended short circuits.
- Impedance Mismatch: Delamination alters the precise dielectric thickness between signal layers and their reference planes. This change directly impacts impedance, degrading signal integrity, especially for high-speed signals, leading to data errors or system instability.
- Intermittent Failures: Delamination can cause connections to break and reconnect intermittently, particularly during thermal cycling, making troubleshooting incredibly difficult.
- B. Mechanical Failures:
- Delamination significantly reduces the structural integrity of the multilayer PCB, making it more susceptible to further physical damage, cracking, or warpage.
- Visible bubbles or blisters can interfere with component placement during multilayer PCB assembly or cause components to detach from the board.
- C. Thermal Degradation:
- Trapped air pockets created by delamination are poor conductors of heat. This reduces the efficiency of heat transfer away from hot components, leading to localized hot spots and potentially premature component failure.
- D. Reduced Product Reliability and Lifespan:
- Ultimately, delamination is often a precursor to catastrophic board failure, leading to costly field failures, product recalls, and significant warranty claims. For any electronic product, reliability is paramount, and delamination directly undermines this.
V. Preventing Delamination: Best Practices for Multilayer PCB Users and Manufacturers
Preventing delamination requires a concerted effort from the design stage through manufacturing and assembly. This is where partnering with a reliable multilayer PCB supplier becomes crucial.
A. Design Considerations:
- Balanced Copper Distribution: Design your custom multilayer PCB with copper distributed as evenly as possible across all layers. This symmetry minimizes internal stresses that can lead to warpage and delamination.
- Material Selection: Work closely with your multilayer PCB manufacturer to choose materials (cores, prepregs) with appropriate Tg, Td, and CTE properties. For lead-free soldering processes, which use higher temperatures, materials with higher Tg are often necessary.
- Stack-up Optimization: A well-optimized stack-up, designed in collaboration with experienced multilayer PCB manufacturers, not only ensures electrical performance but also considers mechanical stability and manufacturability to reduce delamination risk.
B. Manufacturing Process Control (Primarily for Manufacturers, but good for users to know):
- Strict Lamination Process Control: Reputable multilayer PCB manufacturers employ precise control over temperature, pressure, and vacuum profiles during the lamination cycle to ensure complete resin flow, void-free consolidation, and full curing of the prepreg.
- Material Handling and Storage: Proper handling and climate-controlled storage of prepreg and core materials are vital to prevent moisture absorption and degradation before lamination.
- Surface Preparation: Thorough cleaning and proper surface treatment (e.g., black or brown oxide, or alternative adhesion promoters) of inner layer copper are essential for establishing strong, reliable bonds with the prepreg.
- Bake-out Procedures: Manufacturers may perform pre-baking of panels before lamination to remove any residual moisture.
C. Assembly Process Control (Highly Relevant for Multilayer PCB Users):
- Proper Thermal Profiles: During multilayer PCB assembly, carefully adhere to recommended reflow and wave soldering profiles. These profiles are designed to minimize thermal shock and ensure that the board does not experience excessive heat exposure for too long.
- Moisture Sensitivity Level (MSL) Handling: Follow IPC/JEDEC guidelines meticulously for baking, handling, and storing multilayer PCB panels and moisture-sensitive components. This prevents the dreaded “popcorning” effect, where absorbed moisture rapidly expands during soldering, causing delamination.
- Controlled Rework: Minimize component rework whenever possible. When repairs are necessary, use proper thermal management tools and techniques to prevent localized overheating and stress on the laminate.
D. Quality Assurance and Testing:
- Micro-section Analysis: Regular cross-sectional analysis of production samples is an invaluable tool. It allows multilayer PCB manufacturers to visually inspect for internal delamination, voids, resin flow, and overall lamination quality.
- Thermal Stress Testing: Simulating assembly processes (e.g., solder float test, reflow simulation) can identify a board’s susceptibility to delamination under thermal stress.
- AOI (Automated Optical Inspection): Used for detecting visible surface defects like blisters or bubbles that indicate delamination.
- Ultrasonic Inspection (C-SAM): This non-destructive technique uses sound waves to detect internal delamination and voids that are not visible on the surface.
VI. Conclusion: Ensuring Robust Multilayer PCB Performance
The intricate dance of stacking defines the very essence and electrical prowess of a multilayer PCB. It dictates how signals propagate, how power is delivered, and how heat is managed within your electronic devices. Conversely, delamination, a silent and often insidious failure, poses a significant threat to this carefully engineered structure, capable of rendering a sophisticated board utterly useless.
For every user of multilayer PCBs, from designers to product managers overseeing multilayer PCB assembly, understanding both the strategic art of stack-up design and the critical pitfalls of delamination is paramount. By collaborating closely with reputable multilayer PCB manufacturers and multilayer PCB suppliers who employ stringent process controls and robust quality assurance, and by implementing best practices in material handling and assembly, you can significantly mitigate the risk of delamination. Investing in a well-designed and properly manufactured multilayer PCB is not just about building a product; it’s an investment in your product’s long-term reliability, performance, and ultimate success in the market.